Discussion on mixing process control parameters of small internal mixer in laboratory
The mixer is used for the mixing and mixing of rubber, plastic and chemical raw materials, as well as the mixing of various high and low viscosity materials. It is equipped with PLC programmable liquid crystal display, man-machine interface operating system, curve display of the close relationship between temperature, time and torque, and the mixing process is completed automatically. PLC touch screen has USB interface, which can be controlled by computer connection and extract data. It is simple to operate, energy-saving and efficient. It is suitable for formula research and development, research and determination of raw materials in manufacturer's laboratories and scientific research institutions.
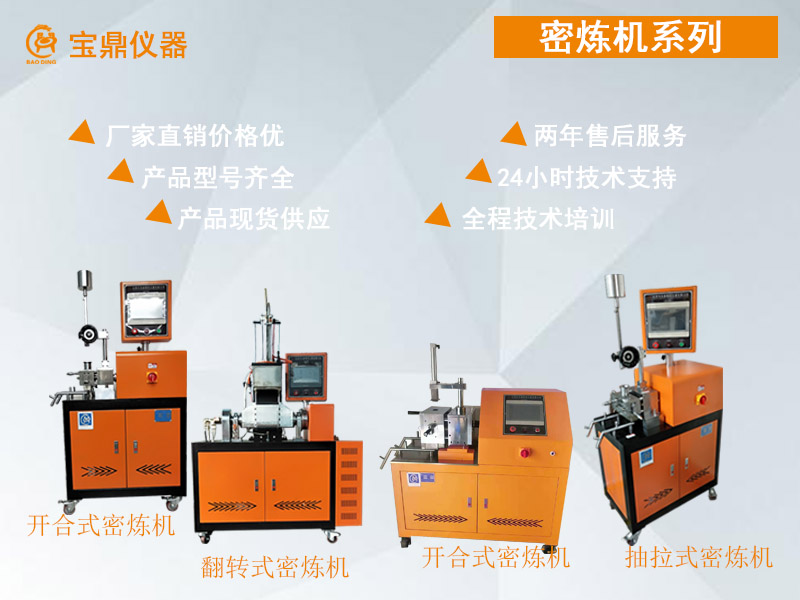
There are four common control parameters of internal mixer: time, temperature, energy and power. Single parameter control or multi parameter control can be adopted. Among the four control parameters, time parameters were mainly used in the early stage, and now temperature and time parameters are mostly used. Relatively few use energy and power parameters.
Temperature control:
In order to ensure the stable quality of each batch of compound. The
internal mixer has been proved to be effective in controlling the material temperature during the mixing process. The temperature is the rubber temperature detected by the temperature sensor in the internal mixer room and in immediate contact with it. Generally, after the raw rubber is put into the internal mixer, the temperature of the feeding point, the temperature of the oil feeding point and the temperature of the rubber discharging point shall be controlled. During the mixing process, the internal mixer rotor shall work on the rubber, Therefore, the whole process of heat generation is a temperature rise process.